Automatically manage your inventory requirements with real time usage and replenishment notifications
Clarendon AIR
Automatic Inventory Replenishment
The innovative Kanban/VMI solution utilising RFID twin-bins. Clarendon AIR provides the capability to automatically manage the inventory requirements of your business through RFID (Radio Frequency Identification) tags which are located in the bin hardware. This provides real time usage for any parts consumed and replenishment notifications transmitted at the touch of a button.
How does it work?
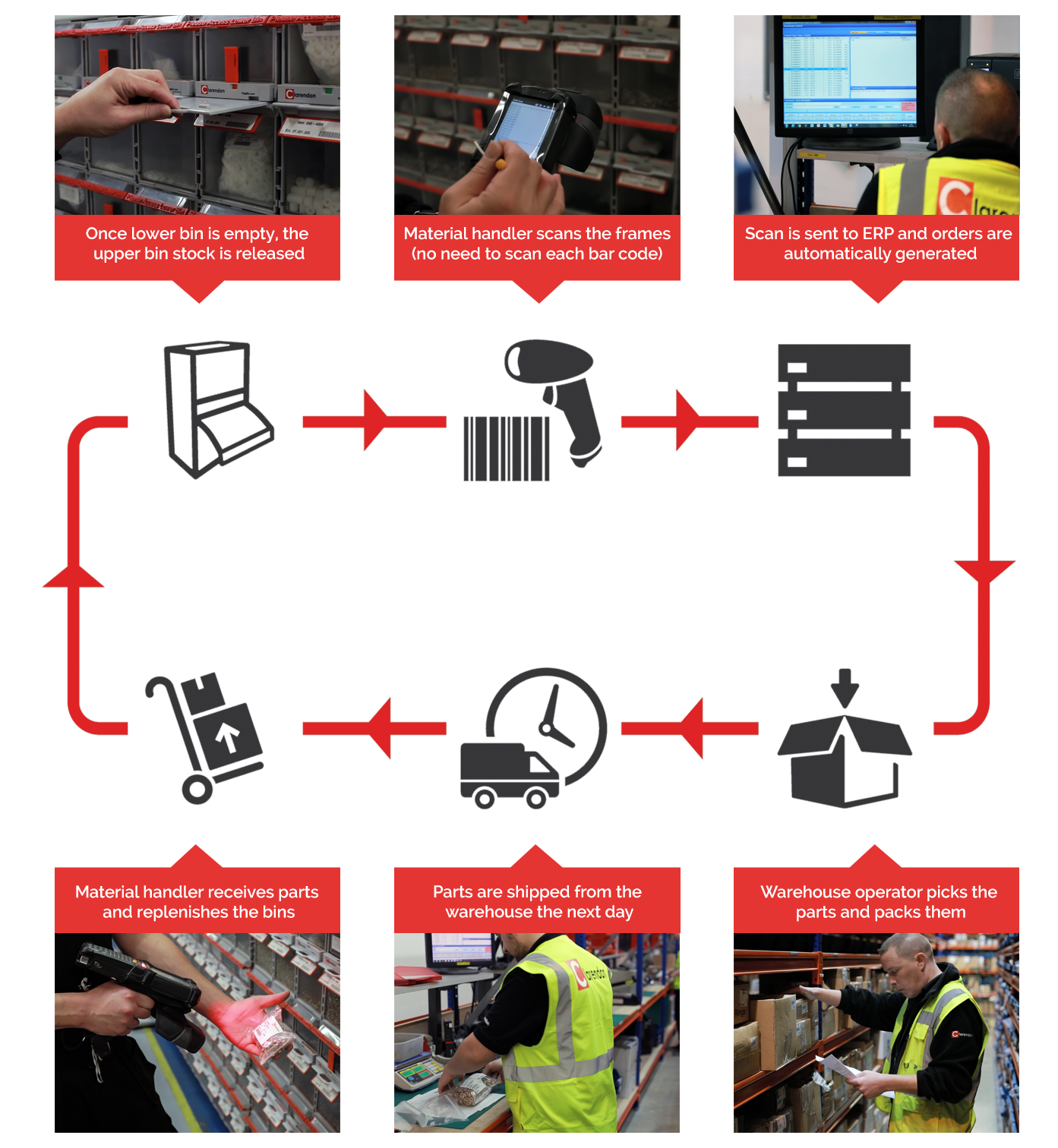
Watch the video
Clarendon Air Inventory System - How it works video
Clarendon AIR Hardware
TWINBIN
- Bottom bin contains loose inventory (owned by customer)
- Top bin contains consignment inventory (owned by Clarendon)
- Free standing standard racking/multi-purpose solutions that can be retro fitted to existing workstations
BAGGED STOCK
- Unique bag ID
- No mixed batches in bag
- Unique barcode
- Customised bag sizes
RFID SCANNER
- No need to scan individual barcode
- Scan range - up to 30ft/9m
- Immediate transmission to Clarendon ERP
Management Software
PORTAL
- Consumption Analysis by part/bin/rack/location
- View/search activity on all live data bins/workstations
- Add bin/replace bin/change quantity functionality
- Various reporting and KPI's (OTD, NCR)
- Paperwork and certificates management
CLARENDON ERP
- Live feed via RFID signal into Clarendon ERP through bespoke technology
- Daily alerts for urgent requirements
- Confirmation of scans via email to dedicated VMI (Vendor Managed Inventory) account manager